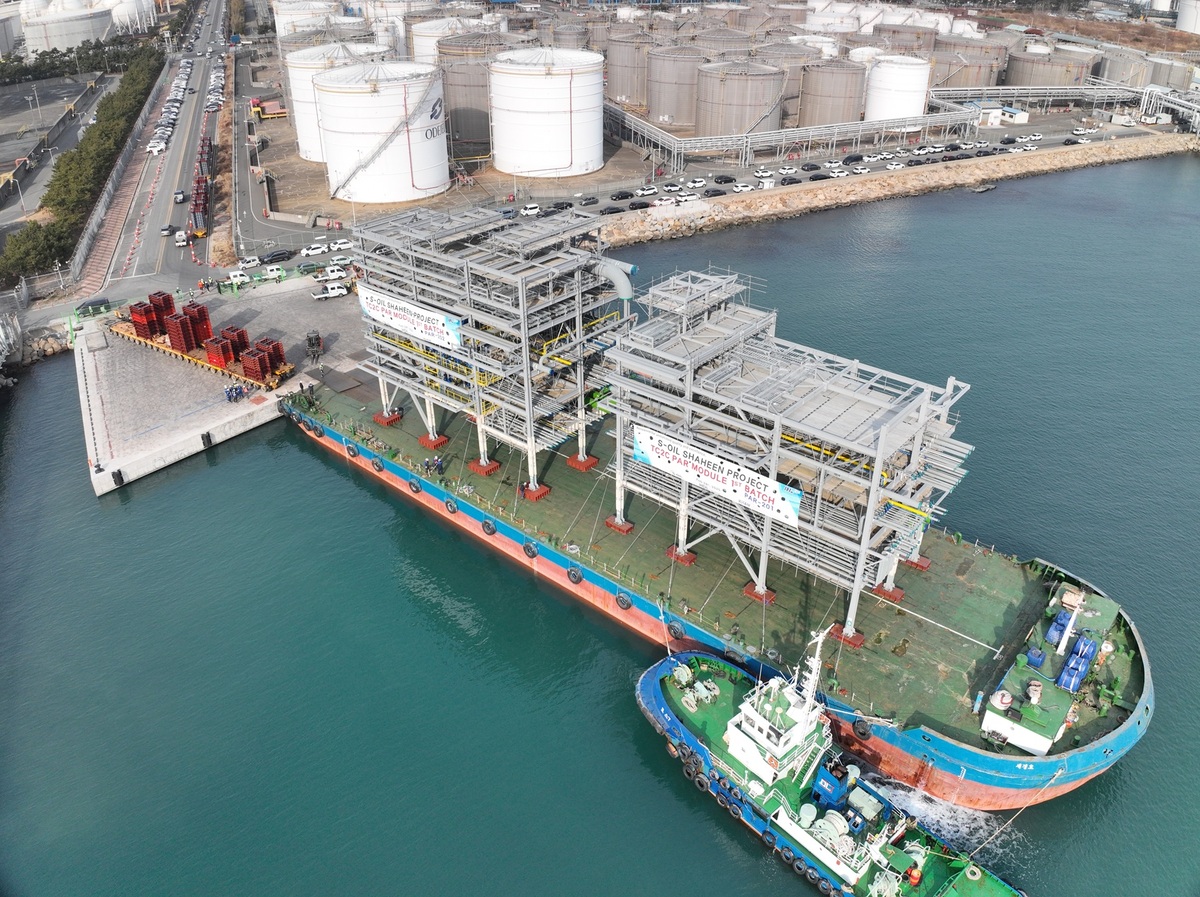
DL이앤씨가 국내 석유화학 업계 사상 최대 규모 투자인 에쓰오일의 ‘샤힌 프로젝트’ 건설 현장에 PAR(Pre-Assembled Pipe Rack) 모듈을 설치했다고 7일 밝혔다.
PAR 모듈은 플랜트의 원료와 생산품 등의 이동 통로 역할을 하는 배관을 지지하는 구조물이다. 이번에 설치한 PAR 모듈은 울산 온산산업단지에 석유화학 시설을 짓는 샤힌 프로젝트를 위해 목포 모듈 제작장에서 옮겨졌다. DL이앤씨는 지난 2월부터 10회에 걸쳐 순차적으로 모듈을 운송했다. 길이 47m, 너비 22m, 높이 36m에 이르는 대형 모듈을 포함해 총 17개다. 옮긴 모듈의 무게는 모두 1만t에 이른다.
모듈의 설치를 위해선 크게 세 가지 작업이 필요하다. 먼저 모듈은 미세한 차이로도 이상이 발생할 수 있어 정확한 제작이 중요하다. 특히 모듈을 제작하는 공간과 이를 설치하는 실제 물리 환경에 차이가 있는 만큼 정확도를 담보하기 어렵다. DL이앤씨는 이 같은 문제를 해결하기 위해 ‘3D 스캐닝’을 도입했다. 3D 스캐닝은 레이저를 발사한 뒤 대상에 부딪혀 돌아오는 시간을 계산해 공간 구조를 파악하는 기술이다. 이 정보를 기반으로 샤힌 프로젝트 현장을 목포 모듈 제작장에 3D로 완벽히 구현해 냈다. 여기에 지형지물을 고려한 맞춤형 모듈 제작이 함께 이뤄졌다. 규격에 딱 맞춰 제작된 모듈 사이 간격은 3㎜를 넘지 않았다. DL이앤씨는 모듈과 모듈 사이에 배관을 넣어줘 어긋난 부분을 맞추는 기존 방식에 비해 공정이나 용접량을 줄일 수 있었다고 설명했다. 용접 한 번으로 모듈을 이어붙이는 SWHU(Single Weld Hook Up) 방식으로 용접량을 50%가량 절감했다는 게 회사 측 설명이다.
그 다음으로는 모듈을 바지선에 실어 울산신항까지 450㎞에 달하는 거리를 운송했는데 이 작업이 쉽지 않았다. 모듈을 옮기는 동안 무게 중심이 수시로 바뀔 수 있어 파손·전복 등의 위험에 노출돼 있기 때문이다. 특히 파도와 바람, 조류의 영향을 받는 장거리 해상 운송은 더욱 정교한 하중 분산이 요구됐다. DL이앤씨는 각 모듈의 체적, 무게 중심에 따라 고박(묶는 작업) 위치를 선정하고, 특수 제작한 받침목과 고정끈으로 포장하는 등 전문적인 해상 운송 엔지니어링 기술을 적용했다.
모듈 설치의 최종 관문은 육상으로 옮기는 작업이다. 울산신항에 도착한 모듈을 샤힌 프로젝트 현장으로 옮길 때는 ‘모듈 트랜스포터(SPMT)’를 동원했다. 모듈 트랜스포터는 주로 조선소 등에서 큰 선박이나 대형 구조물을 옮기는 데 사용되는 특수 운송 장비다. 금속판 아래 바퀴 4개가 달려 있는데 여러 개를 이으면 화물 기차처럼 움직인다. 모듈의 길이를 고려해 한 줄에 6대씩 2줄로 길게 연결했다. 이동 작업은 인적이 드문 야간시간에 진행됐다. 진동을 최소화하는 ‘초저속 운송’으로 모듈을 2㎞ 움직이는 데 2시간이 걸렸다.
모듈 공법은 플랜트 공사에서 새롭게 주목받는 분야 중 하나다. 보통 플랜트 공사는 현지 시공 방식으로 이뤄져 기후·인력 등 현장 여건에 영향을 많이 받는다. 반면 모듈 공법은 기계, 배관 등 설비 구성 요소를 사전에 제작해 문제 발생의 여지를 최소화한다. DL이앤씨는 플랜트 모듈 분야에서 두각을 나타내고 있다. 현재 미국 텍사스주 오렌지카운티에 세계 최대 규모 폴리에틸렌 공장을 모듈 공법으로 짓고 있다. DL이앤씨가 공사한 에쓰오일 잔사유 고도화 시설(RUC)은 단일 모듈로는 국내 최대 무게(3400t) 기록을 세우기도 했다.
DL이앤씨는 총 3개 패키지로 나누어 발주된 샤힌 프로젝트에서 핵심인 ‘패키지 1’을 현대건설·현대엔지니어링과 함께 수행하고 있다. 샤힌 프로젝트는 내년 6월 준공을 목표로 순조롭게 진행 중이다.
유재호 DL이앤씨 플랜트사업본부장은 “석유화학 플랜트 중 샤힌 프로젝트라는 새로운 영역에 진출했다는 점에서 의미가 크다”며 “치밀한 사전 준비와 과거의 모듈 제작·운송 노하우, 전문 인력 덕분에 성공적으로 마무리할 수 있었다”고 말했다.
이정인 기자 lji2018@segye.com